Crafted stories.
Every object has a maker, and every maker has a story. Discover the narratives of emerging and established artists, the evolution of their creations, and how the everyday is made more extraordinary through the fine art of craft.
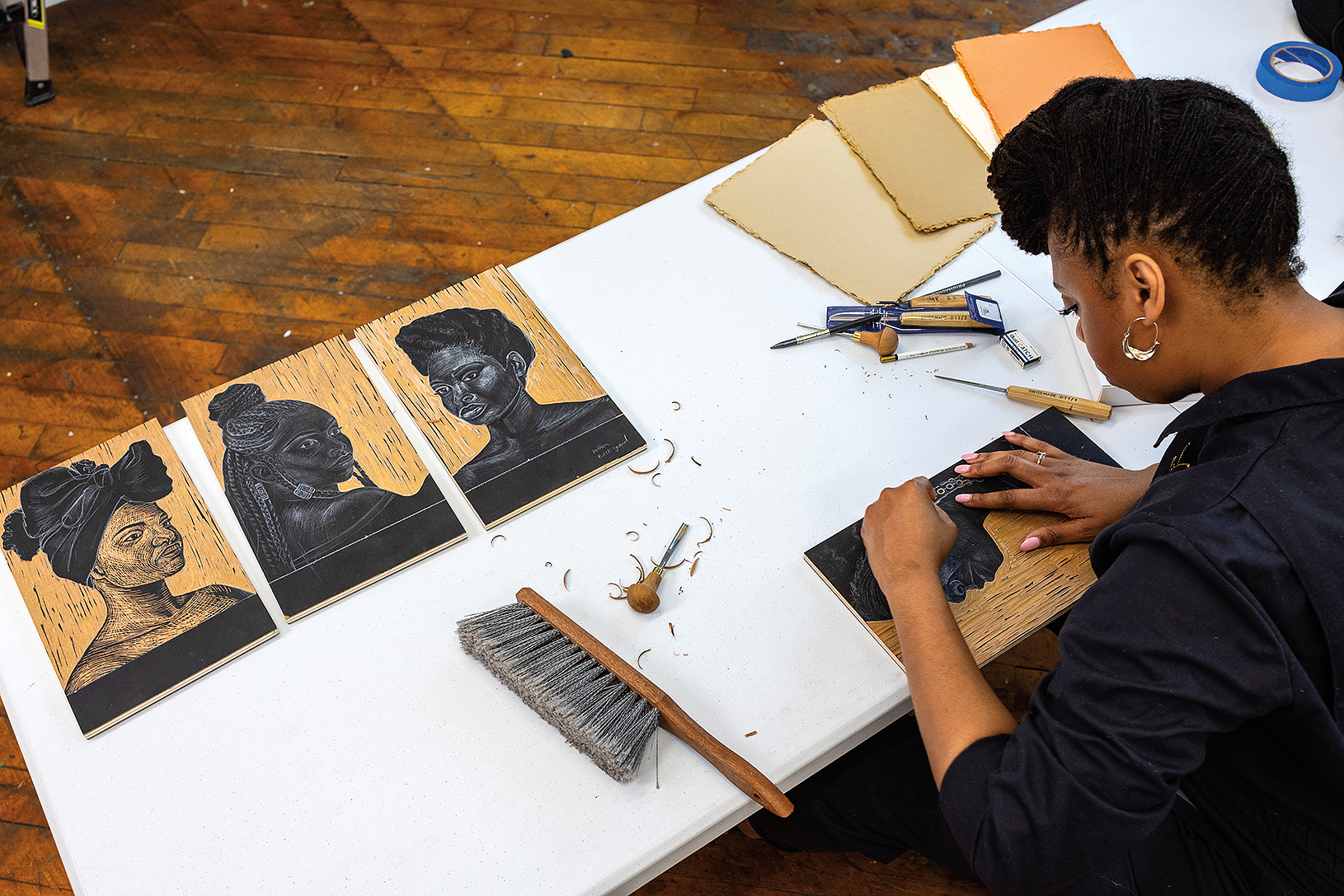
You are now entering a filterable feed of Articles.
273 articles
-
MakersFree To Read
Runway Ready
Metalsmith Thomas Bliven crafts handmade accessories for top-tier clothing labels and the celebrities who make their fashions memorable.
Fall 2025
Features + Profiles -
MakersFree To Read
The Queue: Dawn Williams Boyd
Dawn Williams Boyd fashions recycled textiles into powerful paintings in cloth. In The Queue, the Atlanta-based textile artist talks about her family’s dedication to the handmade, the extensive list of tools that make her work possible, and the importance of senior art programs.
Digital Only
The Queue -
ACC NewsFree To Read
Remembering John McQueen
Conceptual fiber artist and ACC Gold Medalist John McQueen died on July 26, 2025. He redefined the field of contemporary basketry to embrace non-functional sculpture, and explored the concepts of containment and space in his work.
Digital Only
-
Free To Read
-
Free To Read
-
MakersFree To Read
Slow Style: Punch Needle Fashion
Micah Clasper-Torch brings fashion sense to the punch needle revival.
Fall 2025
Features + Profiles -
MakersFree To Read
Where Jewelry People Gather
The Jewelry Library in New York City fosters scholarship and creativity while building community.
Fall 2025
Craft Communities -
MakersFree To Read
All Dressed Up
Inspired by textiles, ceramist Samantha Briegel adorns her work like a stylist.
Fall 2025
Features + Profiles -
MakersFree To Read
From Canvas to Carving
Felicia Greenlee transforms wood into layered narratives that challenge history, celebrate Black identity, and spark conversation through texture and form.
Fall 2025
Features + Profiles
Story categories.
-
Craft Happenings
Browse a timely, curated, and frequently updated list of must-see exhibitions, shows, and other events.
-
Points of View
Essays, craft histories, ideas, analysis, and other perspectives on the significance of craft.
-
Makers
Profiles, interviews, studio tours, and videos on people who are making the world more beautiful.
-
Materials & Processes
Learn about materials and how craftspeople transform them into functional and sculptural works.
-
Handcrafted Living
Discover practical and pleasing handmade goods and stories about living with meaningful objects.
-
Travel
Explore the world of craft by visiting the places and communities where it is created and celebrated.
-
Media Hub
Discover new books, niche periodicals, videos, and podcasts—plus highlights from ACC’s archives.
-
ACC News
Explore the impact of the American Craft Council and the ACC community through stories and updates on our programs, events, artists, and more.
Explore American Craft magazine.
Award-winning journalism in the craft field.
Learn more about one of the country’s leading publications on the diversity of American craft and its makers.
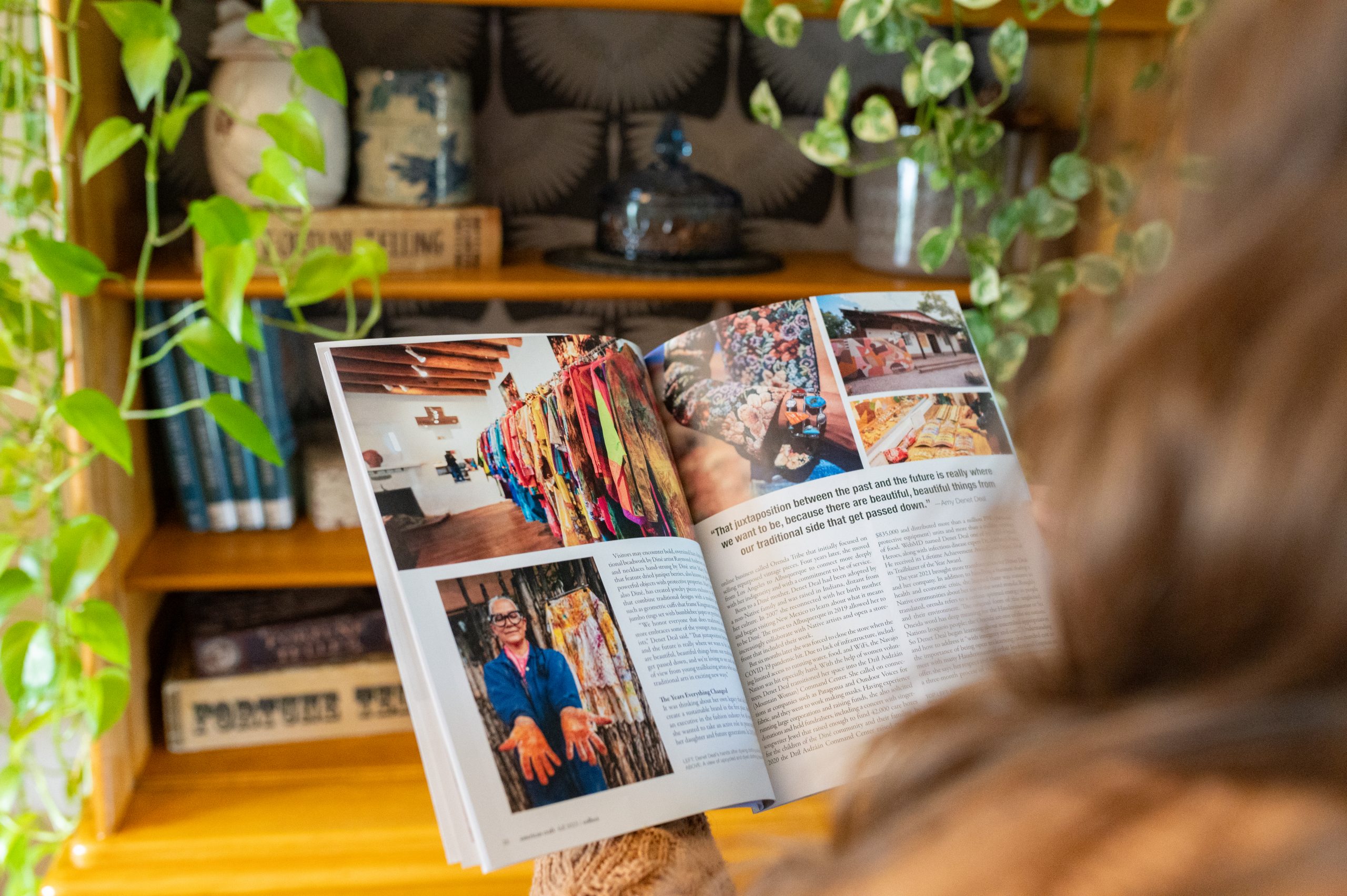
Become a member
Join today and start your craft journey!
Support makers, celebrate the handcrafted, and get American Craft delivered to your home with a membership to the American Craft Council.